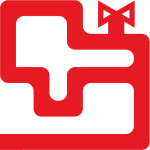
This first Unit introduces “Process safety”. It highlights the importance of this topic from the lessons learnt from major accidents. It then covers some of the most important types of incident observed in the process industries, especially loss of containment, fires and gas phase explosions.
For each type of incident, it gives real examples, together with determining parameters and an outline of methods of prevention and protection.

The second unit continues the presentation of the most important types of incident observed in the process industries. It covers physical explosions, dust explosions and condensed phase explosions, including runaway reactions. For each type of incident, it gives real examples, together with determining parameters and an outline of methods of prevention and protection.
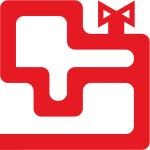
The third unit looks at the various ways to reduce the risk of
incidents. It explains how and why we
draw up plans of classified hazardous areas or “explosive zones” and what we
should do in such areas to reduce the risk level. It covers the control of ignition sources in
order to prevent fires, gas phase explosions and dust explosions. It also covers the issue of pressure and
vacuum relief.
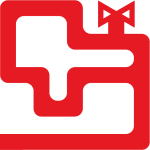
The fourth unit looks at how we estimate the effects of incidents such as leaks, fires and explosions. For a given type of incident, it presents the methods used to estimate distances to pre-defined threshold levels of toxicity, thermal radiation and overpressure. It shows how such studies can help to define the areas where there is a risk of injury or death.

The fifth unit outlines the main methods used to identify hazard scenarios for a given industrial process unit. The methods presented incorporate HAZard and OPerabilty Studies (HAZOP) and Layers of Protection Analysis (LOPA), as used in the Solvay group of companies.
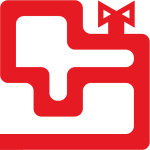
The sixth unit details how we assess the risk level of a hazard scenario in the Solvay group of companies. It shows how we prioritize risk and deal with in a timely fashion. The method we use has some features that are unique to Solvay, but it is still firmly based on the established literature, so the material will be useful to engineers working for other companies.

The seventh unit shows how we carry out a risk assessment of a fire or explosion scenario. It includes how to assess, in a semi-quantitative way, the frequency of potential ignition sources. The ignition sources covered include electrostatic discharges, hot surfaces, electrical equipment, rotating machinery, electromagnetic radiation and lightning. The ignition frequency depends the flammable gas or dust, the extent of the zone where a flammable mixture is present and the type of equipment in that zone.
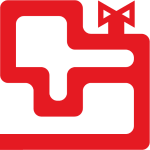
Many engineers work on the same industrial facility. They fulfil a variety of functions: design, commissioning, operation, maintenance, etc., and of course safety. A common modelling means is therefore essential, in particular for ensuring safety. This Unit introduces the Piping and Instrumentation Diagram (P&ID) modelling tool. After clarifying the tagging and shape conventions, examples make it easier to understand the notations and benefits of P&ID.
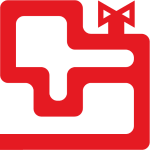
Instrumentation in chemical facilities plays an essential role when implementing safety devices. Sensors communicate the most important physical values either to a control loop to regulate a process (including its shutdown), or to a simple display. Sensors are also a key component of Safety Instrumented Systems (SIS). This Unit addresses the principle of a control loop and the role of sensors. Sensors must be chosen carefully according to the context of their use. The various characteristics enabling the appropriate selection of the following sensors are studied: temperature sensors, pressure sensors, flow rate sensors, and level sensors.